Effectively carry out vehicle component tests with decelerator sleds.
Numerous test scenarios can be realized with decelerator sleds. Advantages over acceleration tests include pre-braking scenarios, easy integration into existing crash systems, and also a direction of movement synchronous to the crash. The test sleds are decelerated either by means of PU tube brakes, bending bar brakes, or more modern servo-hydraulic brake systems. For example, the combination of the MESSRING HydroBrake and the M=SLED test sled can be used to carry out all common component tests and can drive individual complex crash pulses.
Tests with deceleration sleds generally follow a set procedure: the test object is mounted on a rail-guided sled platform, which is driven by a motor system up to the impact speed before the braking device applies the deceleration pulse. The required pulse is generated during braking; servo-hydraulic systems such as the MESSRING HydroBrake outperform PU and bending bar brakes in terms of test preparation time, reproduction of deceleration pulses, and the possible speed curve.
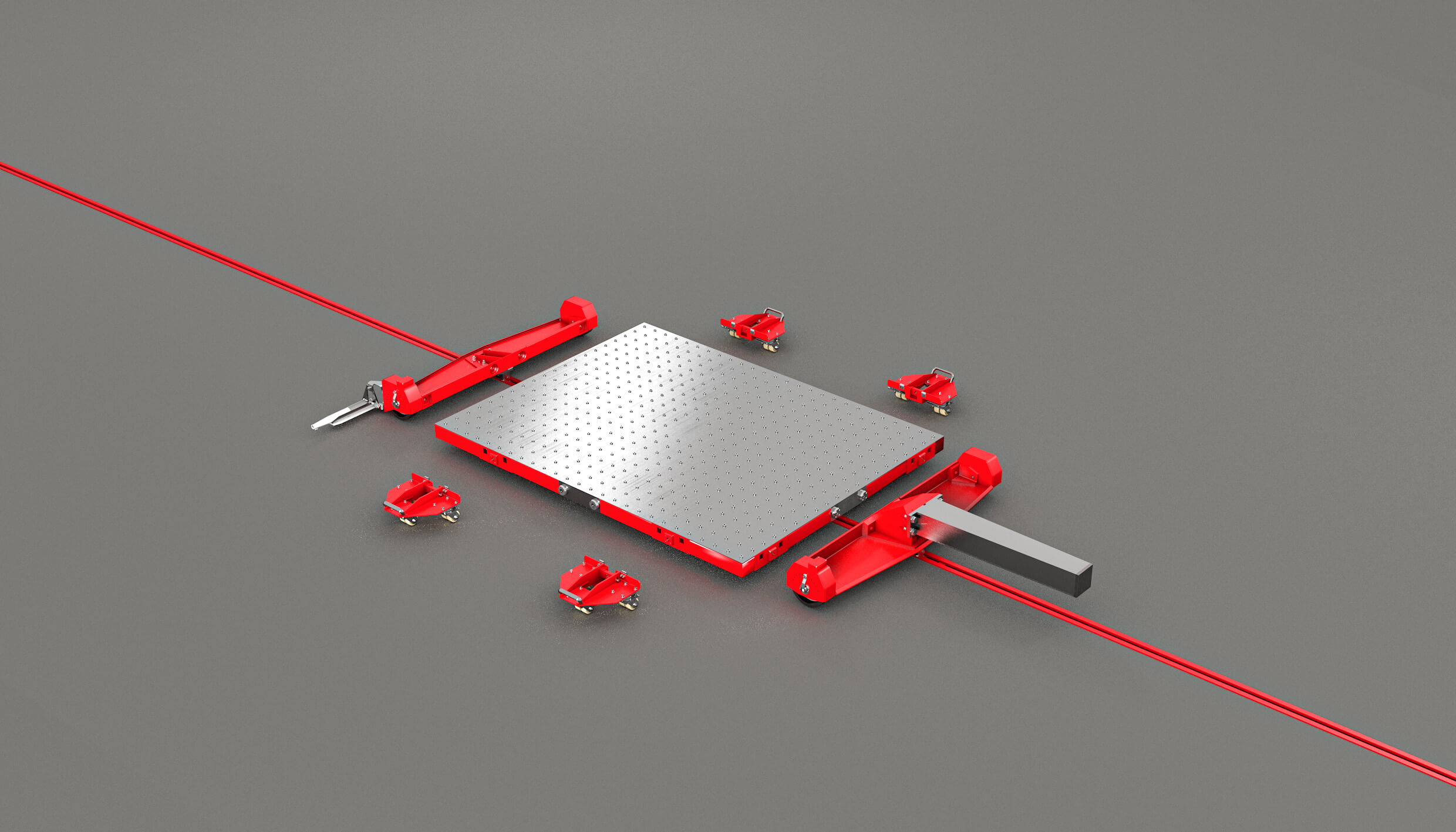
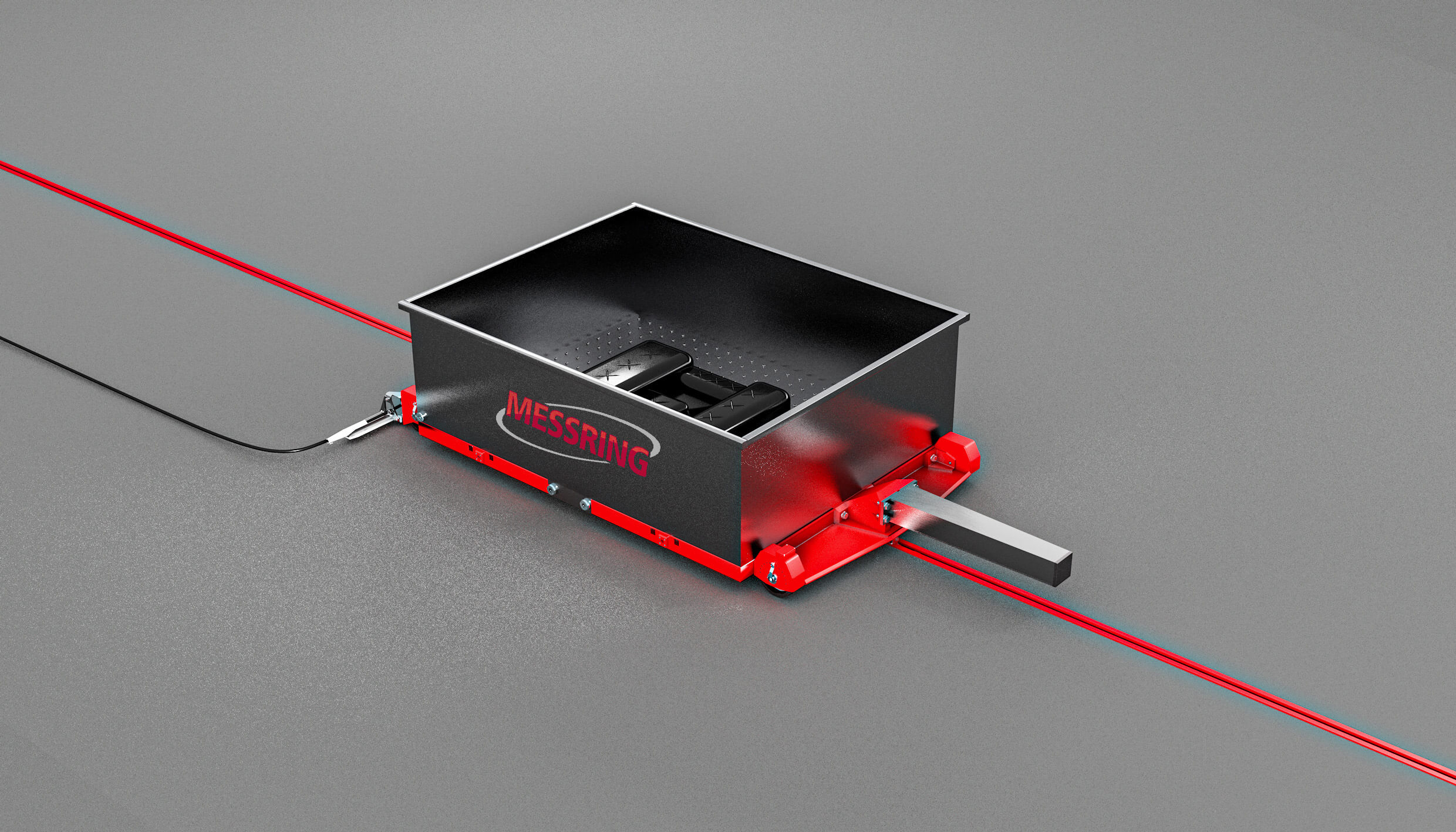
M=SLED
Different types of sleds are used for different test object and protocol requirements. M=SLED sets the standard for the requirements in this segment. With its compact dimensions and mounting surface of 2,800 mm x 1,800 mm, this sled allows high payload and is ideally suited for most standard tests. In operative test handling, the sled exhibits perfect running smoothness thanks to its height adjustment to the rail and thus the precise maintenance of the dummy position as well as the rearly and laterally arranged surfaces for data acquisition devices and other instrumentation. Suitable sled superstructures are available for test requirements according to ECE R16, R129, R44, and ADAC front and side impacts and can be easily mounted on the existing mounting grid.
M=SLED XL
The trend towards ever-larger vehicles is taken into account with the offer of the M=SLED XL. It combines a mounting surface of 4,000 mm x 1,800 mm with all the advantages of the M=SLED and enables large-scale non-destructive tests. Furthermore, with the M=SLED XL, a rotated test or vehicle body setup of up to ±29° around a central anchored pin is feasible.
M=SLED Modular
The newly developed M=SLED Modular heralds a new era in terms of flexibility in sled testing. As the name suggests, the sled has a modular design: the two-piece undercarriage supports various modules in its center, which can be easily exchanged. At present, two platforms are available: a module with the standard 2,800 mm x 1,800 mm mounting grid and a container module specifically adapted to potential fire hazards encountered in battery tests. Both modules are compatible with undercarriages in the longitudinal as well as transverse directions.
The M=SLED Modular opens up completely new options in the test sequence. By exchanging modules in just a few simple steps, test series with different superstructures can be pre-assembled and the utilization of the system can be optimized. Measuring devices can remain on the prepared module and only need to be connected and disconnected. uring battery tests that check whether the insides of batteries suffer critical internal damage even under high acceleration, the stainless steel tray installed in the container module prevents any potential uncontrolled spread of fire. Furthermore, in the event of fire, the module can easily be separated from the undercarriage and brought to a suitable place for extinguishing or controlled burning. The mandatory testing of batteries in the X and Y axes is also easy to implement thanks to the option of rotating the whole module by 90°.
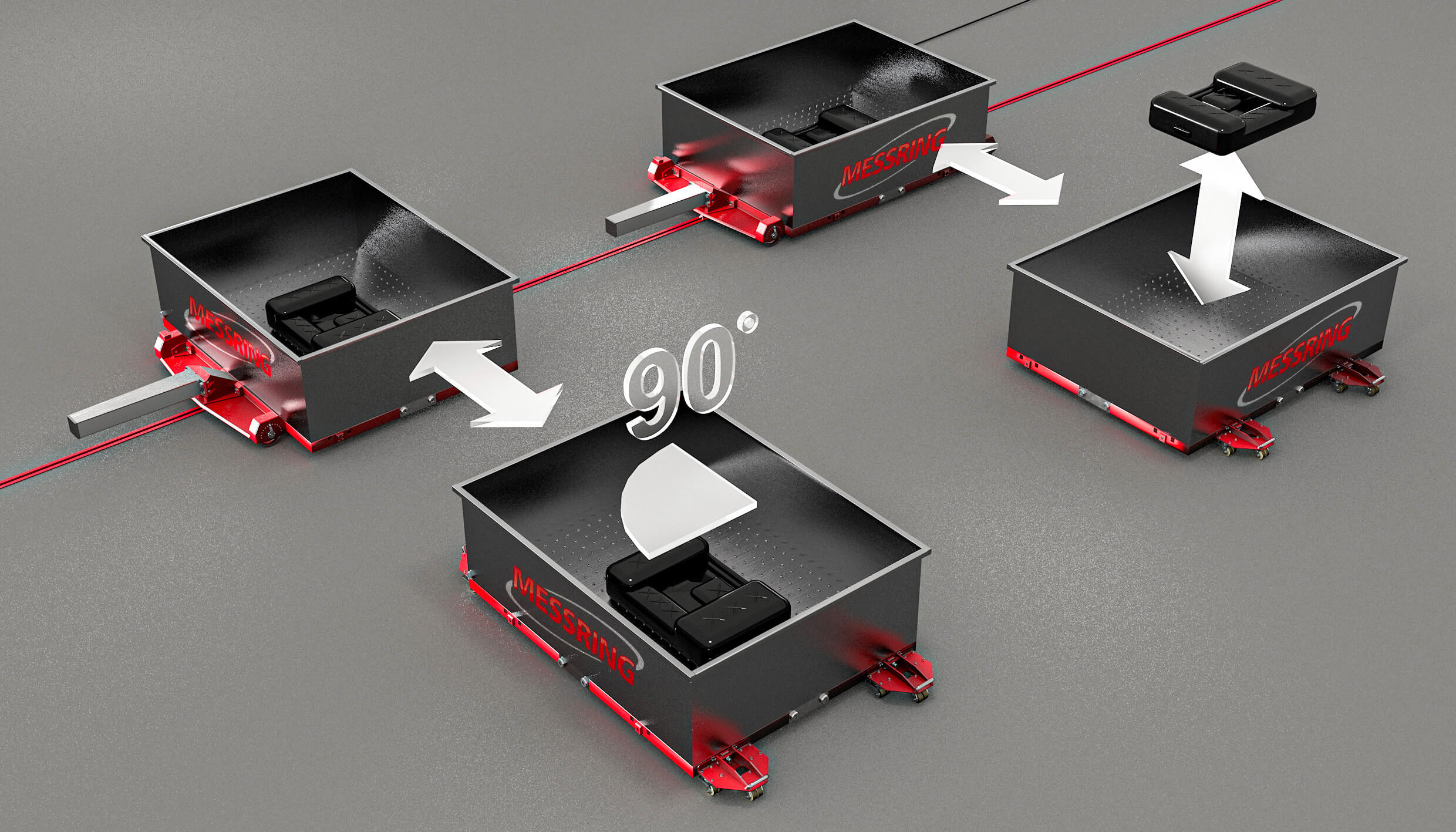