Batteries are playing an increasingly important role in the automotive industry. Electric vehicles are on the rise and the integral safety of batteries is a key issue in the development of new vehicles. MESSRING as a leading provider of crash testing equipment, offers customized solutions and tools for testing batteries and battery packs. These include standard tests such as the ECR R100 with the Compact Impact Simulator (CIS), extreme abuse tests with up to 150 g load in special sled tests as well as crash tests of large-sized electric vehicles.
Type Approval
The ECR R100 is an international standard test. One core criterion, with particular relevance to crashworthiness, is the so-called mechanical shock included in the standard. The purpose of this test is to reproduce the inertial loads in longitudinal and transverse directions that may occur in a vehicle crash. The MESSRING Compact Impact Simulator allows to exactly reproduce the required forces and accelerations applied to the battery. The highly efficient system impresses with pin-point pulse modeling, integrated data acquisition and short set-up times. The perfect test system to run series and quality tests while meeting the high requirements for repeatability and data acquisition.
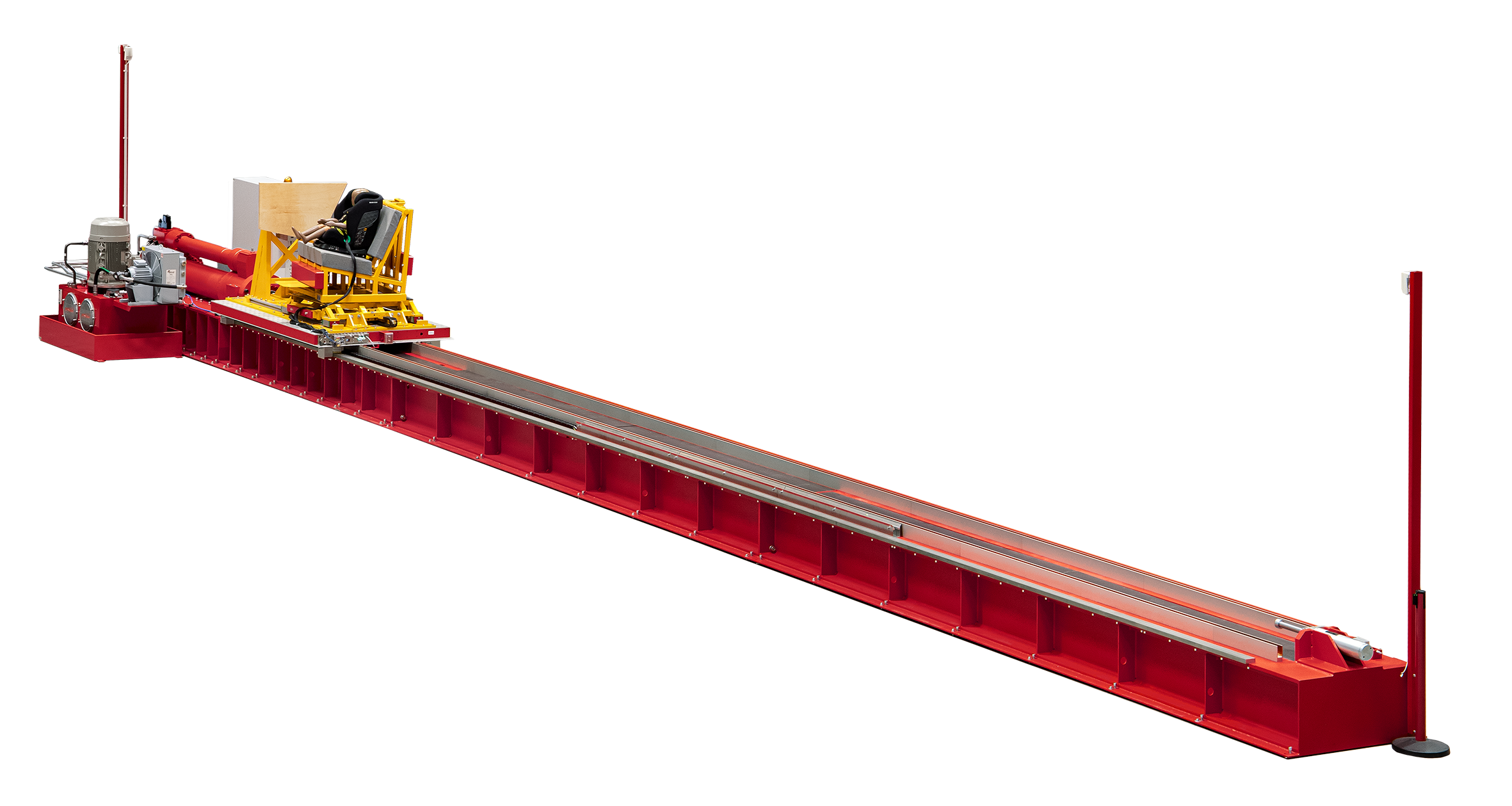
Abuse Testing
More extreme tests to evaluate the resilience of batteries at their limits can be achieved with PU, bending plate or servo-hydraulic braking systems such as the MESSRING HydroBrake. Loads of up to 150 g are achieved in this way and test whether batteries still function under extreme conditions and do not pose a danger. MESSRING has developed a test sled specifically tailored to the requirements of battery tests. The M=SLED Modular, trimmed for lightweight construction, has a container module to hold the test object. The container prevents uncontrolled fire spread in the event of a thermal runaway and can be flooded with extinguishing water to contain a fire incident. The module can be easily separated from the chassis and is mountable in longitudinal and transverse direction. This means that testing of the batteries can be implemented in the X and Y axes and, in the event of a fire, the damaged battery can be evacuated easier.

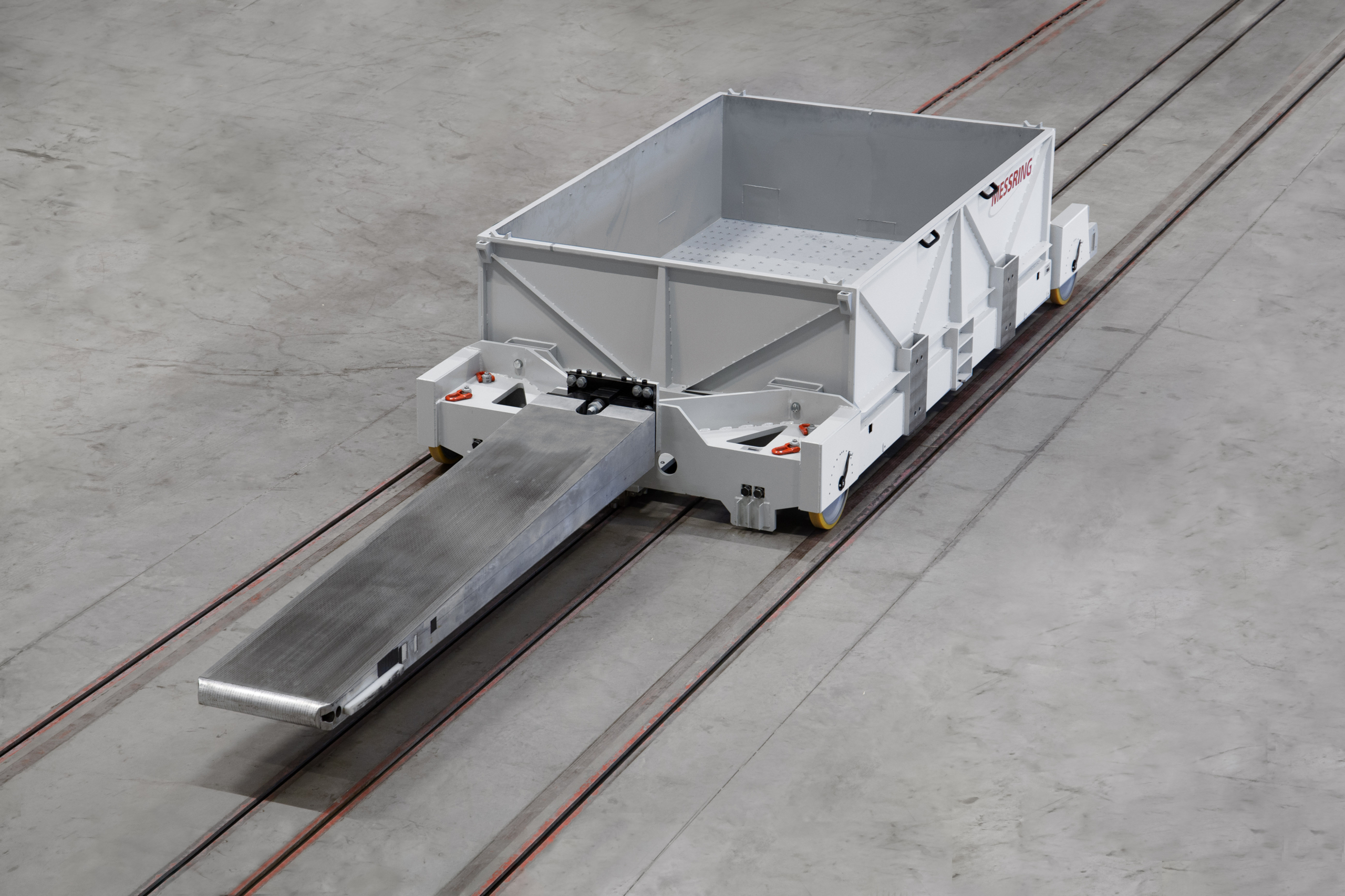
High mass – high impact force
Another challenging test setup is the side pole impact test. In this test, an electric vehicle is mounted on a so-called flying floor sled and fired at 32kp/h onto the instrumented pole. The force acting on the battery is immense and places the highest demands on the internal stability and safety of the battery pack and the structural connection such as the frame and mountings. The high mass of the electric vehicles with huge trajectory battery packs and the associated impact force prompted the crash test experts at MESSRING to develop the new M=WALL Strong. The enhanced loadcell measures forces and moments precisely in five axes and with up to 550 kN. This means that even peak loads, such as those described in the pole impact, can be monitored. In addition, the cell can be flexibly instrumented to almost any other barrier and provides reliable data acquisition for a wide range of applications.
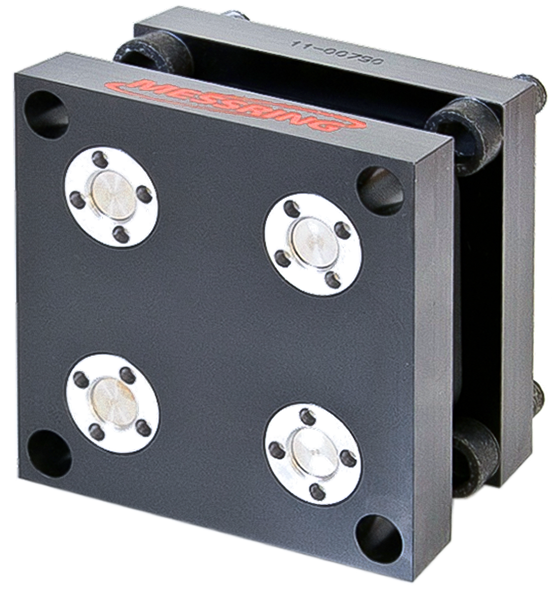